Dialing in the perfect print settings is the cornerstone of achieving consistently high-quality 3D prints. While your printer and filament choice lay the groundwork, it’s the fine-tuning of slicer parameters—layer height, print speed, temperature, and support structures—that transforms good prints into flawless masterpieces. Whether you’re troubleshooting stringing, improving surface finish, or boosting strength in functional parts, a handful of smart lifehacks can streamline your workflow and save you filament (and time). This guide dives into actionable tips for adjusting key slicer and filament settings so you can elevate your prints from draft quality to professional-grade with minimal trial and error.
Understanding Layer Height and Print Speed
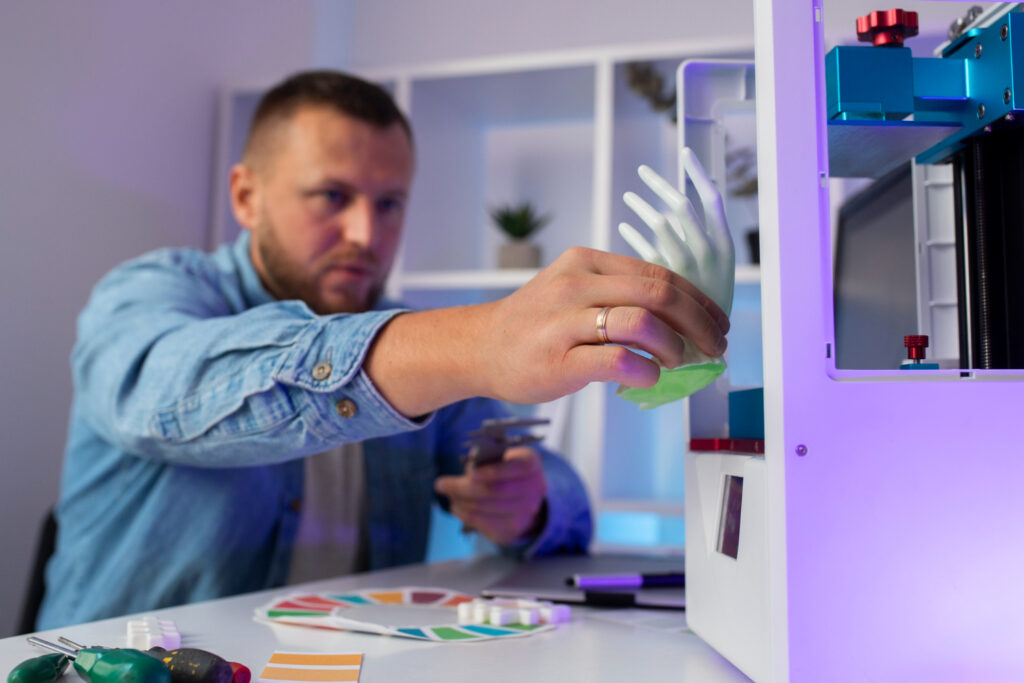
Layer height dictates the resolution and smoothness of your prints. Lowering the layer height (for example, from 0.2 mm to 0.1 mm) reduces the visibility of layer lines but increases print time. A good lifehack is to match the layer height to at most 75% of your nozzle diameter—so with a 0.4 mm nozzle, cap layers at 0.3 mm. This balance preserves detail without dramatically prolonging prints. Print speed also affects surface quality; if you notice ringing or ghosting artifacts around corners, try reducing speed by 10–20% in your slicer’s “Print Speed” slider. For complex geometry, enable dynamic speed adjustment so the firmware automatically slows down on small layers. These tweaks help you maintain smooth curves and crisp edges without resorting to excessively slow, time-consuming profiles.
Mastering Temperature Control
Temperature plays a pivotal role in layer adhesion, dimensional accuracy, and cosmetic finish. Too low, and the filament won’t bond properly, leading to delamination; too high, and you’ll get excessive stringing and blobbing. A simple lifehack is to print a temperature tower—a calibration model divided into zones where each zone prints at a different temperature (e.g., 190 °C, 200 °C, 210 °C, and so on). Inspect the finished tower to pinpoint the sweet spot where layers fuse cleanly without visible strings. Once identified, enter this temperature into your slicer’s material settings. Additionally, enable “Variable Nozzle Temperature” in advanced slicers to drop the extrusion temperature during travel moves, reducing oozing without compromising layer adhesion.
Optimizing Support Structures and Adhesion
Support settings can make or break complex overhangs and bridging. Rather than using the slicer’s default dense supports everywhere, apply custom support placement: enable “Support Blockers” to remove supports from flat areas and “Support Enforcers” only under steep overhangs. Choose a lower “Support Interface Density” (around 20%) and a thicker “Interface Layer Height” to facilitate easy removal and smoother undersides. For bed adhesion, switch from a glass plate to a PEI sheet or apply a thin layer of gluestick on the build surface. Another lifehack is to print a brim of 3–5 mm width for small or tall parts to prevent corner lifting, then peel it off once the print is complete.
Tuning Retraction and Flow Settings
Stringing and blobs often stem from suboptimal retraction and flow rates. Start by enabling retraction: set a “Retraction Distance” of 4–6 mm for Bowden setups or 1–2 mm for direct-drive extruders, with a “Retraction Speed” of around 40–60 mm/s. Print a small retraction test model to fine-tune these values until strings between pillars disappear. Next, calibrate your flow rate (also called “extrusion multiplier”) by measuring the weight of a known-length filament extrusion: adjust the flow in your slicer until the measured output matches the expected weight within 1 %. This ensures the right amount of plastic is deposited, eliminating over-extrusion that causes gobs and under-extrusion that leads to gaps.
Final Checks and Iterative Improvements
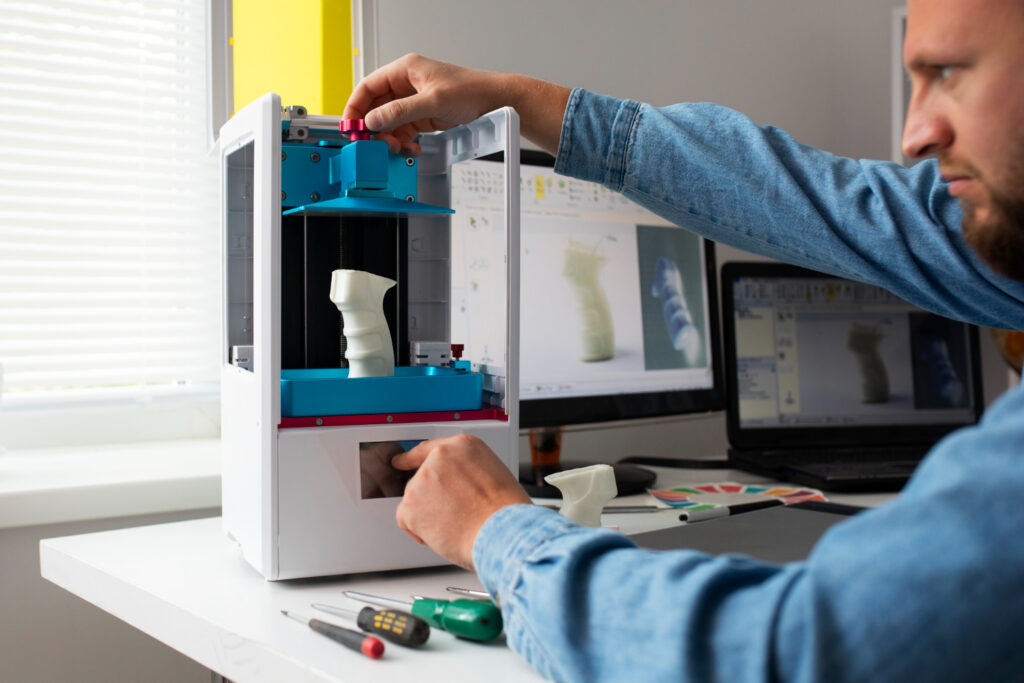
After applying these lifehacks, always run a small calibration print—such as a 20 mm cube with features like overhangs and bridges—to verify your settings. Document each change in a simple spreadsheet: record the parameter, its value, and print outcome (e.g., “no stringing,” “smooth surface,” “good adhesion”). This systematic approach helps you revert to known good settings if future filament changes or model geometries introduce new challenges. By iteratively refining your slicer profile and leveraging targeted lifehacks, you’ll consistently achieve sharp details, clean surfaces, and robust parts—turning mundane prints into reliable, high-quality creations.
Leave a Reply